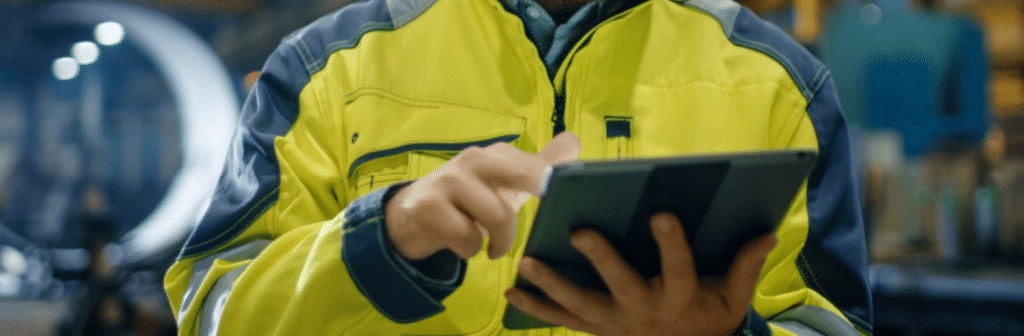
Maintaining accurate records of lifting equipment inspections is a fundamental aspect of health and safety management in the UK.
Proper record-keeping not only ensures compliance with legal requirements (PUWER and LOLER) but also promotes a culture of safety within an organisation.
Legal Requirements for Record Retention
The Health and Safety Executive (HSE) provides guidelines on the retention periods for various health and safety records. While specific retention periods can vary depending on the type of record and industry regulations, a general rule of thumb is to retain most health and safety records for at least five years. This duration accounts for potential legal claims, as civil claims for injury can be made up to three years after an incident.
What Affects Retention Periods?
Several factors determine how long inspection records should be kept:
- Legal and Regulatory Requirements: Certain records may have statutory retention periods defined by law.
- Industry Standards: Some industries have specific guidelines or standards that dictate retention periods.
- Organisational Policies: Companies may establish internal policies that extend retention periods beyond legal requirements to support operational needs or historical reference.
Lifting Operations and Lifting Equipment Regulations 1998 (LOLER) Requirements
Under the Lifting Operations and Lifting Equipment Regulations 1998 (LOLER), it’s essential to maintain thorough records of all examinations and inspections of lifting equipment to ensure safety and compliance.
Regulation 11 of LOLER specifies the requirements for record-keeping:
- Initial Thorough Examination:
- Lifting Equipment: Keep the report for the entire duration the equipment is in use, unless an EC Declaration of Conformity is available.
- Lifting Accessories: Retain the report for at least two years.
- Periodic Thorough Examinations:
- Maintain these reports either until the next examination report is created or for a minimum of two years, whichever is longer.
- Examinations After Exceptional Circumstances:
- If equipment undergoes examination due to circumstances that could affect its safety (for example, after an incident or significant modification), keep these reports for the same duration as periodic examinations.
For more detailed guidance, please refer to the HSE’s publication on Thorough Examination of Lifting Equipment.
Provision and Use of Work Equipment Regulations 1998 (PUWER) Requirements
The Provision and Use of Work Equipment Regulations 1998 (PUWER) mandate that employers ensure work equipment is suitable, maintained, and inspected to safeguard health and safety. While PUWER does not specify exact retention periods for records, maintaining detailed documentation of equipment inspections, maintenance, and risk assessments is essential for demonstrating compliance and ensuring workplace safety.
Best Practices for Record Retention under PUWER:
- Inspection and Maintenance Records: Retain these records for the expected lifespan of the equipment. This practice ensures that a comprehensive history is available, which is crucial for ongoing safety assessments and any potential audits.
- Risk Assessments: Keep records of risk assessments for as long as they remain relevant, especially if they inform current safety procedures or relate to equipment still in use.
- Training Records: Document and retain records of employee training on equipment use for the duration of their employment, ensuring proof of competence and compliance with safety protocols.
By adhering to these practices, employers can effectively demonstrate compliance with PUWER and uphold a safe working environment.
Best Practices for Record Management
To ensure effective management of inspection records, we’d recommend considering the following tips:
- Develop a Retention Schedule: Outline how long each type of record should be kept, considering legal obligations and organisational needs.
- Regularly Review and Update Policies: Periodically assess and update retention policies to stay aligned with current laws and industry best practices.
- Secure Storage: Store records securely, whether in physical or digital format, to prevent unauthorised access or damage.
- Proper Disposal: Once records have surpassed their retention period, dispose of them securely to maintain confidentiality and comply with data protection regulations.
Adhering to these guidelines will help ensure compliance with LOLER and PUWER, as well as creating a safer working environment for all.
Why not make examination/inspection record keeping easy? Our very own Kinetic helps to keep you on top of inspections at all time. Get in touch to learn more.