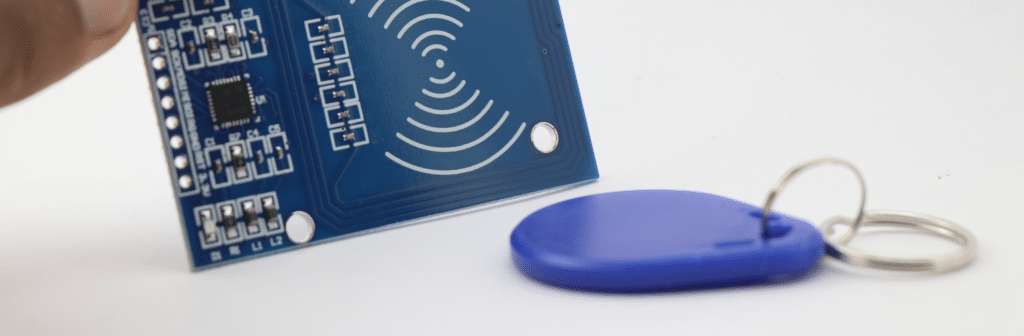
In our ever-changing world, businesses are always on the lookout for new technology to boost efficiency and ensure high standards of safety.
One technology making a big impact in equipment inspections is Radio-Frequency Identification (RFID).
In this blog post we will dive into how RFID is revolutionising the way we inspect equipment, bringing accuracy, speed and cost-effectiveness to the forefront.
What is RFID Technology?
RFID works by using electromagnetic fields to identify and track tags attached to specific items or equipment. These tags hold information that RFID readers can wirelessly retrieve almost like magic – items communicate with readers without needing to be directly scanned.
Using RFID in Equipment Inspections
Traditional equipment inspections often involve manual data entry and piles of paperwork, leading to errors and delays. But with RFID, we can change that.
Improving Accuracy: RFID tags can store detailed information about equipment, from maintenance history to inspection schedules. This means inspectors get all the facts straight, reducing the chances of mistakes.
Smoother Inspections: Using RFID makes finding equipment a breeze. No more hunting around searching for items – RFID readers do the hard work, leaving inspectors to focus on what matters most.
Cost Savings All Around: Efficiency equals savings. With RFID, we can cut inspection times, reduce errors and keep our equipment running smoothly – all while saving money.
RFID in Action
Imagine a manufacturing plant using RFID to streamline equipment inspections. By tagging machinery and using RFID readers during inspections, they’ve made inspections a lot faster and more accurate. The result? Less downtime, fewer errors and happier inspectors.
RFID can change the game in equipment inspections. It’s giving us the tools to work smarter, not harder – and that’s something we can all get behind.
Challenges of RFID Technology
As much as RFID technology can aid and enhance equipment inspections, it can also present a few challenges. As RFID tags are often concealed or protected, inspectors often have difficulty locating tagged items as precise positioning is necessary for successful detection. Additionally, reading RFID tags may require supplementary equipment, such as an external device connected to a compatible iPad device. These factors highlight just a few of the challenges of using RFID technology for equipment inspections.
Embracing RFID in Your Inspections
If your business is looking to embrace RFID and take inspections to the next level, get in touch for a chat to discover why Motion’s dedicated inspection and reporting software Kinetic is the right choice for you. We don’t lock you to a single RFID provider, meaning you are free to choose the best product, price and supplier for your business needs. With Motion Kinetic and RFID, the future is bright.